OSHA has reportedly fined a grain handling facility fined $721,000 after a worker was engulfed in a storage bin. The OSHA news item reports as follows:
"OSHA fined Cooperative Plus Inc. $721,000 after a near tragedy in February, when a worker in a storage bin was trapped in soybeans up to his chest in 25 degree weather. The worker was ultimately rescued after a four-hour ordeal. OSHA issued 10 citations against the Burlington, Wis., farmer-owned cooperative after inspectors concluded that the employer had willfully disregarded safety requirements by exposing workers to the risk of being engulfed and suffocated in grain storage bins. Two of the citations were for multiple egregious violations for failing to provide workers entering grain storage bins with body harnesses and lifelines and failing to provide an observer while other workers entered the grain bins. See the news release for more information about this case and OSHA's new grain storage bins fact sheet* for more information on engulfment hazards".
Unfortunately, this type of incident happens with disturbing frequency in the grain handling industry. In the last 10 months, OSHA fined two grain handling facilities more than $3 million after separate incidents in which a 17-year-old who had just graduated high school and a 52-year-old husband and father were engulfed and suffocated in grain storage containers. Last month, two Illinois teenagers (ages 14 and 19) were suffocated after being engulfed in a grain bin they had entered. A third young worker was hospitalized after being trapped in the bin for 12 hours.
OSHA has published a useful fact sheet on the hazards in silos, which is given in this link
August 17, 2010
August 15, 2010
Gas cylinder explosion incident
Treat your gas cylinders with respect. The Gas cylinder Rules are very clear in specifying the safety precautions to be taken. Gas cylinders not properly handled are ticking time bombs. An incident of gas cylinder explosion killing one person in Pune has been reported and the plant manager has been arrested. Please see the news articles in these links:
Gas cylinder explosion
Plant manager arrested
Gas cylinder explosion
Plant manager arrested
Process Safety Management - Its not all technical!
A huge wave of interest in Process safety generally occurs after a major incident. The Jaipur oil fire,the BP oil spill, the Bhopal gas disaster court verdict and other incidents have sparked a huge interest in process safety.The management of process safety does require a lot of technical competence. However the MANAGEMENT of Process Safety requires just that - its about people. Just pause back a bit - Bhopal - 1984.... reasons for the incident - cost cutting without assessing risks, ignoring warnings,poor emergency response planning... the list goes on. One or more of the same reasons keep coming up for the recent incidents also! Technology has changed rapidly and we have Safety Integrity levels, redundant systems, more reliable equipment etc etc but still accidents happen. Why? Because wrong decisions are taken by a human being. Whatever administrative frameworks we design and provide for risk based process safety, one day a human being is going to override the administrative framework and take a decision that ultimately causes an incident. I was jokingly mentioning to participants of a process safety seminar that as long as people exist, the job of a process safety management consultant will be in demand!Have a safe day!
August 14, 2010
Fire in Plastics Godown in Kolkata
Thanks to Abhay Gujar for sending news about a major fire in a plastics godown in Kolkata. Do we give the same importance for emergency preparedness to godowns and warehouses that store hazardous materials as we do for chemical manufacturing units? See a video of the fire in this link.
August 12, 2010
6 workers drown in Lucknow Ketchup Factory
Alas, it's happened again. A worker fell into a ketchup tank in a ketchup factory in Lucknow, India. In the process of trying to save her, another 5 co-workers lost their lives. In any confined space entry, the job of the man watch is to call for help if anybody inside needs to be rescued. Train your operators on rescue techniques and most importantly train them to overcome the natural feeling of going inside the confined space without proper protection to rescue a fallen co-worker.
Read more of this incident in this link.
Read more of this incident in this link.
August 11, 2010
Dangers of chemical reactions
Unexpected chemical reactions are dangerous and can kill.Whenever a new product is envisaged, it must be taken through a proper management of change process, including understanding of process chemistry.Even though this incident happened in 2008, it underscores the importance of knowing what you are doing. Read about the incident in this link.
More recently, another accident occurred at a chemical factory at Ankleshwar where two people died. Read about the incident in this link.
More recently, another accident occurred at a chemical factory at Ankleshwar where two people died. Read about the incident in this link.
OSHA will not ban Gas Blowing of pipelines
A news article in the Wall street journal mentions the following: "OSHA administrator David Michaels, in a news briefing Thursday, said his agency is putting the power industry "on notice that it is inherently dangerous" to conduct gas blows and he said the industry "must assure worker safety," if it persists.
But he said he wouldn't put an emergency order in place that would prohibit gas blows until the agency studies it further. "We would love to be able to ban it, but we can't," he said.
The chairman of the Chemical Safety Board, which investigated the incident, said Thursday that OSHA's response to the Kleen Energy explosion was insufficient despite it being even though it is the third-largest recommended fine in a single accident in agency history.
"I believe there should be an emergency response to an emergency situation," said Rafael Moure-Eraso, the board's chairman, a former academic.
After the board's probe, big equipment makers including General Electric Co. and Siemens AG said they would tell their customers to substitute compressed air or nitrogen for natural gas. Utility American Electric Power also said it would avoid the procedure based on the board's findings and its own analysis".
Read the full article in this link.
But he said he wouldn't put an emergency order in place that would prohibit gas blows until the agency studies it further. "We would love to be able to ban it, but we can't," he said.
The chairman of the Chemical Safety Board, which investigated the incident, said Thursday that OSHA's response to the Kleen Energy explosion was insufficient despite it being even though it is the third-largest recommended fine in a single accident in agency history.
"I believe there should be an emergency response to an emergency situation," said Rafael Moure-Eraso, the board's chairman, a former academic.
After the board's probe, big equipment makers including General Electric Co. and Siemens AG said they would tell their customers to substitute compressed air or nitrogen for natural gas. Utility American Electric Power also said it would avoid the procedure based on the board's findings and its own analysis".
Read the full article in this link.
August 9, 2010
Fire in chemical godown at Bangalore
Thanks to Mr Sritharan for sending the following information:
Please find the news on the fire which broke out in a chemical (solvents and thinners) storage godown in Shivajinagar, Bangalore. The godown was located in a densly populated commercial and residential area. As usual the fire dept says that the godown did not have the necessary license only after the incident and do not have proper procedures to check out these violators.
Also the news reports that the local people started pouring water as soon as they saw the fire without knowing that some water sensitive chemicals can indeed aggrevate the situation. Only the trained fire fighters should handle these types of chemical fires.
Read the news article in this link.
Please find the news on the fire which broke out in a chemical (solvents and thinners) storage godown in Shivajinagar, Bangalore. The godown was located in a densly populated commercial and residential area. As usual the fire dept says that the godown did not have the necessary license only after the incident and do not have proper procedures to check out these violators.
Also the news reports that the local people started pouring water as soon as they saw the fire without knowing that some water sensitive chemicals can indeed aggrevate the situation. Only the trained fire fighters should handle these types of chemical fires.
Read the news article in this link.
August 8, 2010
Where does the buck stop in Process Safety Management?
I have been viewing the numerous developments in process safety in India with great interest. The Indian Chemical Council has taken a big interest in Process Safety and is collaborating with the Center for Chemical Process Safety of the US. While it is good that a great awareness of Process Safety Management is being created in India, where does the buck stop as far as Process Safety Management goes? The composition board of directors of many chemical organisations in India are changing with fewer and fewer companies having technically qualified people at the helm.With due respect to the immense experience that other directors bring, I see an erosion in technical competence at the board level. While risk based process safety does bring in process safety metrics to the board's attention, it needs technical competence to analyse these metrics. Ultimately, the culture of the organisation trickles down from the decisions that the board takes. What is the long term solution to this issue? No amount of management systems is going to avoid a catastrophic incident. They will warn you adequately before a big incident happens, but unless someone at the board level is competent to analyse these warnings, you cannot prevent the incident. It boils down to basic human behaviour. Is a director on the board going to pay more attention to what another technically competent director is saying, or to the various process safety metrics he sees displayed but may not fully understand? I leave it to you to decide...
Meanwhile read an interesting article in the Fortune magazine in this link.
Meanwhile read an interesting article in the Fortune magazine in this link.
August 6, 2010
Drum bursting hazard - readers innovation
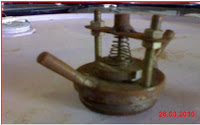
In my earlier post , I had mentioned an incident on the dangers of pesticide technical drums bursting when placed in a hot box or steam heated bath. A couple of readers Mr P.Kadhiravan and Mr P.Thulasiraman of Coromandel International Limited have devised a simple pressure relief system for the technical drums which they place in a steam bath for melting. Their pressure relief device is screwed on to the drum in the bung area after removing the drum cap. A photo of their innovation is shown. Kudos to them! And thanks to them for sharing this information.
Share your incidents!
I thank readers of this blog for their continued support. I request readers to send in short descriptions of process incidents they know, to me at bkprism@gmail.com for publication in the blog. I will give the reader credit for the input. The company's name need not be mentioned.Thanks in advance!
August 3, 2010
Enforcing Process Safety Management
I always wonder that even in the US where PSM is mandatory and companies face stiff fines, there are always violations taking place. Recently OSHA has proposed to fine a seafood company a total of $279,000, for deficiencies in its process safety management program. "The inspection identified other PSM hazards that resulted in 12 serious citations, with $84,000 in proposed fines. These conditions included failing to update process safety information, conduct an incident investigation of a January 2001 ammonia leak, certify or evaluate the PSM program every three years as required, establish and implement procedures to maintain changes in the process, and provide and document employee training".
Read the full article in this link
Read the full article in this link
Subscribe to:
Posts (Atom)