After the BP Texas disaster in 2005, the then CEO of BP Lord John Browne resigned and Mr Tony Hayward took over. An article mentions the following: 'When Mr. Hayward took over BP's leadership from John Browne three years ago this week, the company was at one of the lowest points in its history: badly run, accident-prone and accused in the aftermath of a deadly explosion at its Texas City refinery of putting profits before safety. Mr. Hayward turned BP around, boosting production, cutting costs and significantly reducing on-the-job injuries. Mr.Hayward set about radically simplifying the company and cutting costs. Senior executives were cut by a quarter. In all, 6,500 people, or just under 10% of its work force, lost their jobs. Last month, he was confident enough to talk of an irreversible "change of culture" at BP.None of that seems to matter now, as BP heads into the crisis grinder that has chewed up big names like Toyota and Goldman Sachs. And with about 5,000 barrels of oil leaking from the damaged well each day, Mr. Hayward knows it".
Read more about this interesting article in this link.
Read about the mitigation efforts in this link
May 9, 2010
Process safety information and BP incident
A number of articles are going around on the BP oil spill incident. In one of them, a whistleblower is supposed to have raised safety concerns about BP Atlantis, the world’s largest and deepest semi-submersible oil and natural gas platform. In this article it mentions the following "It was then that the whistle-blower, who was hired to oversee the company’s databases that housed documents related to its Atlantis project, discovered that the drilling platform had been operating without a majority of the engineer-approved documents it needed to run safely, leaving the platform vulnerable to a catastrophic disaster that would far surpass the massive oil spill that began last week following a deadly explosion on a BP-operated drilling rig.
BP’s own internal communications show that company officials were made aware of the issue and feared that the document shortfalls related to Atlantis “could lead to catastrophic operator error” and must be addressed.“The risk in turning over drawings that are not complete are: 1) The Operator will assume the drawings are accurate and up to date,” the email said. “This could lead to catastrophic Operator errors due to their assuming the drawing is correct,” said Duff’s email to BP officials Bill Naseman and William Broman. “Turning over incomplete drawings to the Operator for their use is a fundamental violation of basic Document control, [internal standards] and Process Safety Regulations.” Read more of this article in this link.
BP’s own internal communications show that company officials were made aware of the issue and feared that the document shortfalls related to Atlantis “could lead to catastrophic operator error” and must be addressed.“The risk in turning over drawings that are not complete are: 1) The Operator will assume the drawings are accurate and up to date,” the email said. “This could lead to catastrophic Operator errors due to their assuming the drawing is correct,” said Duff’s email to BP officials Bill Naseman and William Broman. “Turning over incomplete drawings to the Operator for their use is a fundamental violation of basic Document control, [internal standards] and Process Safety Regulations.” Read more of this article in this link.
May 2, 2010
BP Oil Spill
The latest BP oil spill in the Gulf of Mexico could turn out to be bigger than the Exxon Valdez spill. The President of the US himself has flown to Louisana for a first hand look. One would have thought that after the BP Texas Disaster in 2005, many checks and balances would have been put to prevent another disaster. We will have to wait and see the results of the investigation...
See photos of the spill in this link
See photos of the spill in this link
May 1, 2010
Process safety in batch operations
What goes around comes around! As far as process safety incidents in batch process go, I sometimes despair whether we will ever learn from previous incidents. Last year I had investigated some batch process incidents, the causes of which are very very familiar - incompatibility,scale up issues, heat removal issues, MSDS issues and raw material storage issues. For those of you working in the batch process industry, the UK Chemical Reaction Hazards Forum is a good place to get information on batch incidents. Share these incidents with your operating personnel and check whether it could happen in your organization. For further details go to this link.
What I learnt in Process Safety – A tribute to my senior managers at Madras Fertilizers Ltd
32 years ago, I joined the ammonia plant in Madras Fertilizers as a graduate engineer trainee and then went on to be shift in charge and assistant manager in the ammonia plant. The lessons I learnt in process safety from the senior management* are still fresh in my mind. There was no PSM system, no ISO 14001, no OHSAS 18001, but in the ten years I was there, there was no serious process safety incident!
The senior management then were all experts in plant operation and maintenance – you could not fool them! Their decisions were taken appropriate to the risk involved and clearly communicated. They also made sure that critical jobs which had a process safety issue were always supervised by them by giving clear instructions and follow up. This way we knew when we were going off track and correct ourselves before anything happened. They were true “managers” – who played the fine line between process safety and production with such a finesse, you could not but admire and learn from them.
We did take a lot of “process safety risks” when there was a situation, but it was a calculated and clearly communicated risk – with the result, we were always under control.
Cut to today – Today in many plants, there are distinct gaps between what senior management think what is going on as far as process safety is concerned and what is actually happening at the ground level. Why is this happening? My own understanding of the situation leads to the following:
1.Some of the senior management do not have an understanding of the plant – they may be qualified MBA’s but in a chemical plant, what matters most at senior management level is their conceptualization of key process safety risks!
2.Many Senior management do not want to hear “bad news” related to process safety but welcome “bad news” related to sales and profits. I compare the senior management I started my career with many of the senior management today – the difference is that “bad news related to process safety” used to be ferreted out by the senior management I worked with, even though I may think it was not necessary to tell them!
3.Many boards of directors in present chemical companies do not have a clear understanding of the difference between process safety and occupational health and safety.
4.Senior management are led astray by the numerous certifications of ISO 14001/OHSAS18001 etc. leading to a false sense of complacency.
5.Many of the reactions of management today after a process safety incident are of a knee jerk reaction. A comprehensive long term approach is lacking. Everyone wants to safeguard their remaining time with the organization!
*I pay a strong tribute to my former senior managers at MFL: (Late) Mr P.N.Arunachalam, Mr Jacob Eapen, Mr N.Gajendran and (Late) Mr S.Rangaiah
The senior management then were all experts in plant operation and maintenance – you could not fool them! Their decisions were taken appropriate to the risk involved and clearly communicated. They also made sure that critical jobs which had a process safety issue were always supervised by them by giving clear instructions and follow up. This way we knew when we were going off track and correct ourselves before anything happened. They were true “managers” – who played the fine line between process safety and production with such a finesse, you could not but admire and learn from them.
We did take a lot of “process safety risks” when there was a situation, but it was a calculated and clearly communicated risk – with the result, we were always under control.
Cut to today – Today in many plants, there are distinct gaps between what senior management think what is going on as far as process safety is concerned and what is actually happening at the ground level. Why is this happening? My own understanding of the situation leads to the following:
1.Some of the senior management do not have an understanding of the plant – they may be qualified MBA’s but in a chemical plant, what matters most at senior management level is their conceptualization of key process safety risks!
2.Many Senior management do not want to hear “bad news” related to process safety but welcome “bad news” related to sales and profits. I compare the senior management I started my career with many of the senior management today – the difference is that “bad news related to process safety” used to be ferreted out by the senior management I worked with, even though I may think it was not necessary to tell them!
3.Many boards of directors in present chemical companies do not have a clear understanding of the difference between process safety and occupational health and safety.
4.Senior management are led astray by the numerous certifications of ISO 14001/OHSAS18001 etc. leading to a false sense of complacency.
5.Many of the reactions of management today after a process safety incident are of a knee jerk reaction. A comprehensive long term approach is lacking. Everyone wants to safeguard their remaining time with the organization!
*I pay a strong tribute to my former senior managers at MFL: (Late) Mr P.N.Arunachalam, Mr Jacob Eapen, Mr N.Gajendran and (Late) Mr S.Rangaiah
April 30, 2010
Process safety and security
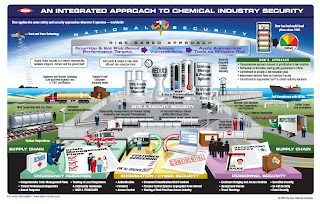
Dow Chemicals has beautifully pictured their "integrated approach to chemical security management" on their website in this link
I wonder when India will really wake up to chemical security threats and bring in legislation and enforce it. With the threats of naxalites and external terrorists and the fact that a number of hazardous chemical units are based on the coast,it becomes imperative that a coordinated approach to chemical plant security is implemented. Let us not wait for an attack to happen!
Fire at Pharma Plant at Ankleshwar
An article in economic times mentions the following "A fire at pharmaceutical major Wockhardt’s Rs 300-crore Ankleshwar facility damaged one of its six manufacturing plants. It will take six months to recommission the unit, a company spokesman said.
The incident adds to the woes of a debt-laden Wockhardt, which had defaulted on payment of its overseas convertible bonds last year, and was forced to accept a corporate debt restructuring package that included sale of some company assets". Read the full article at this link.
While the cause is being investigated, it must be remembered that when companies go under loss, it requires a great effort to maintain safety systems.
The incident adds to the woes of a debt-laden Wockhardt, which had defaulted on payment of its overseas convertible bonds last year, and was forced to accept a corporate debt restructuring package that included sale of some company assets". Read the full article at this link.
While the cause is being investigated, it must be remembered that when companies go under loss, it requires a great effort to maintain safety systems.
April 29, 2010
Process safety - uncomplicate things!
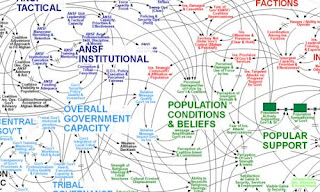
In the Times of India April 28,2010, an article mentions that powerpoint is the US military's new enemy - A general is reported to have said "When we understand that slide (seen above), we would have won the war"! The same general has said that "Its dangerous because it can create the illusion of understanding and the illusion of control". Now what does this have to do with process safety? It is the same as the complicated powerpoint! Just because you perform a complex PHA, SIL study or conduct a management of change study does not mean everything is in control. I have seen many incidents occur even though such studies were conducted. Be practical while conducting these studies and do not go overboard!
April 28, 2010
Process Safety and Overflow protection
I read a nice article on high integrity overflow protection. In the article there is a statement that one of the key requirements of a high integrity overfill protection self certification program is "Acknowledged competency to review the design aspects of both mechanical- and/or electrical-components including component failure modes, fail-safe vs. fail-danger, any claimed automatic diagnostics, and internal redundancy in order to produce a quantitative failure rate (This number will eventually plug into calculations that determine if a particular design meets its defined SIL requirements".
I have observed many SIL (Safety Integrity Level) studies where the above competency becomes suspect. Many organisations think that just because they have completed a SIL study, they are safe. A SIL study starts from a good PHA (Process Hazard Analysis) study and here itself, if the competency of the people participating in the study is inadequate, then "garbage in, garbage out".
In many cases, there has been an overkill of recommendations from a SIL study, leading to the organization spending money unnecessarily.
Read more of the article in this link
I have observed many SIL (Safety Integrity Level) studies where the above competency becomes suspect. Many organisations think that just because they have completed a SIL study, they are safe. A SIL study starts from a good PHA (Process Hazard Analysis) study and here itself, if the competency of the people participating in the study is inadequate, then "garbage in, garbage out".
In many cases, there has been an overkill of recommendations from a SIL study, leading to the organization spending money unnecessarily.
Read more of the article in this link
Process Safety in LPG storage
At Vishakapatnam, the storage of LPG is being done in underground caverns as well as mounded storage. The underground storage facility is an engineering feat by itself.
"A safe method for the storage of large quantities of LPG is Cavern storage. In this method, LPG is stored in mined/artificial caverns at a depth of 160 m to 200 m below the sea level. Cavern is subjected to an external pressure by the saturated rock around the surface, which facilitates in the containment of LPG. The cavern storage is economical only for storage capacities above 50,000 mt and is feasible subject to the suitability of the rock, proximity to the ports with infrastructure for LPG receipt".
A nice description of the cavern is given by the company in this link.
For a draft paper on its construction and other details, please see this link.
HPCL, Visak has also constructed mounded storage of LPG. An article mentions that "Mounded storage of LPG i.e. creating a sand mound around the LPG storage vessels, which are placed above the ground level, is now increasingly being considered by HPCL as the best solution for protecting LPG vessels from BLEVE.
The mounded storage system provides the following advantages:
LPG stored in the form of mounded storage totally eliminates the possibility of BLEVE. The sand cover of 1 metre, which provides natural insulation from external heating, is adequate to outlast any fire in the surrounding areas. Water cooling systems are not required.
In addition, the mounding material provides good protection against most of the external influences like flying objects and pressure waves from explosions".
Read more of the article in this link
"A safe method for the storage of large quantities of LPG is Cavern storage. In this method, LPG is stored in mined/artificial caverns at a depth of 160 m to 200 m below the sea level. Cavern is subjected to an external pressure by the saturated rock around the surface, which facilitates in the containment of LPG. The cavern storage is economical only for storage capacities above 50,000 mt and is feasible subject to the suitability of the rock, proximity to the ports with infrastructure for LPG receipt".
A nice description of the cavern is given by the company in this link.
For a draft paper on its construction and other details, please see this link.
HPCL, Visak has also constructed mounded storage of LPG. An article mentions that "Mounded storage of LPG i.e. creating a sand mound around the LPG storage vessels, which are placed above the ground level, is now increasingly being considered by HPCL as the best solution for protecting LPG vessels from BLEVE.
The mounded storage system provides the following advantages:
LPG stored in the form of mounded storage totally eliminates the possibility of BLEVE. The sand cover of 1 metre, which provides natural insulation from external heating, is adequate to outlast any fire in the surrounding areas. Water cooling systems are not required.
In addition, the mounding material provides good protection against most of the external influences like flying objects and pressure waves from explosions".
Read more of the article in this link
April 26, 2010
Process Safety Information
I was reading an article where it mentions that a company in the USA was penalized for not having proper process safety information. Specifically the article mentions the following:
"The piping system was not provided with labels to indicate the contents or direction of flow. The proposed penalty is $5,600.
• The process safety information pertaining to the equipment in the process did not include the piping and instrument diagrams. The proposed penalty is $5,600.
• The process hazard analysis did not address the hazards of the process. The proposed penalty is $5,600.
• The standard operating procedures for the anhydrous ammonia rail car offloading rack did not address how the operator was to inspect the coupling or ensure that the coupling was serviceable. The proposed penalty is $5,600.
• The employer did not establish and implement written procedures to maintain the ongoing mechanical integrity of process equipment. The proposed penalty is $5,600.
• The ammonia offloading rack, including the coupling on the liquid ammonia offloading arm, had threads that were worn, resulting in the coupling coming apart, releasing more than 8,000 pounds of ammonia.
• The alarm system for evacuation voice alert was unintelligible in all locations within buildings on the plant site. The proposed penalty is $2,400".
Read the complete article in this link.
"The piping system was not provided with labels to indicate the contents or direction of flow. The proposed penalty is $5,600.
• The process safety information pertaining to the equipment in the process did not include the piping and instrument diagrams. The proposed penalty is $5,600.
• The process hazard analysis did not address the hazards of the process. The proposed penalty is $5,600.
• The standard operating procedures for the anhydrous ammonia rail car offloading rack did not address how the operator was to inspect the coupling or ensure that the coupling was serviceable. The proposed penalty is $5,600.
• The employer did not establish and implement written procedures to maintain the ongoing mechanical integrity of process equipment. The proposed penalty is $5,600.
• The ammonia offloading rack, including the coupling on the liquid ammonia offloading arm, had threads that were worn, resulting in the coupling coming apart, releasing more than 8,000 pounds of ammonia.
• The alarm system for evacuation voice alert was unintelligible in all locations within buildings on the plant site. The proposed penalty is $2,400".
Read the complete article in this link.
April 22, 2010
Process Safety - Effects of a Natural gas line rupture
Belgium's worst ever industrial disaster occurred on on July 30, 2004. At about 8:30am local time, people felt a strong smell of gas. The gas was leaking from an underground natural gas pipeline. Emergency responders arrived and were clearing the area when the gas caught fire and exploded. The official death toll was reported as 24. Please see graphic descriptions of the incident and its effects in this link.
Process Safety - oil rig explosion
An explosion has been reported at an oil rig contracted by BP. It appears that the CSB is considering investigating this incident. Please read full article in this link.
April 18, 2010
Process Safety and the Union's view
I read an interesting article about Process Safety and behaviour based safety and the unions perspective on it.In India, behaviour based safety is being bandied about by many as the ultimate solutions to all problems. Organisations have to understand that not only is the worker's behaviour responsible, it is also the behaviour of the top management that is also responsible for process safety!
Read the full article by the Steelworkers union in this link
Read the full article by the Steelworkers union in this link
April 10, 2010
Process Safety and Albert Einstein!
I read an interesting quote by Albert Einstein - " Only two things are infinite - the universe and human stupidity. And I am not so sure about the former."
Now how does this apply to Process Safety? Time and again, we see human errors and human factors being the root cause of incidents! The incidents I investigate tell me that Einstein is laughing in his grave! Will we ever learn from our past mistakes?
Lets wait and keep our fingers crossed.
Now how does this apply to Process Safety? Time and again, we see human errors and human factors being the root cause of incidents! The incidents I investigate tell me that Einstein is laughing in his grave! Will we ever learn from our past mistakes?
Lets wait and keep our fingers crossed.
Process Safety - Fire at Ankleshwar plant
A fire occurred at a pharma company in Ankleshwar. "The blaze at pharmaceutical major Wockhardt Ltd’s factory in Ankleshwar on Saturday was brought under control today. Additional fire tenders had to be called in from Vadodara, Ahmedabad and Surat and kept on standby.
“The fire was almost brought under control last night, but due to leakage of certain chemicals, there was re-ignition in some parts of the factory. The fire was completely extinguished by Sunday evening,” said Manoj Kutariya, Manager, Fire Safety, Disaster Prevention and Management Centre. . Read more in this link.
Just last month, there was a fire in another unit at Ankleshwar. I had visited the Disaster Prevention and Management Center about 6 months back and I was very impressed with the facilities and the team headed by Mr Manoj. Kudos to them.
“The fire was almost brought under control last night, but due to leakage of certain chemicals, there was re-ignition in some parts of the factory. The fire was completely extinguished by Sunday evening,” said Manoj Kutariya, Manager, Fire Safety, Disaster Prevention and Management Centre. . Read more in this link.
Just last month, there was a fire in another unit at Ankleshwar. I had visited the Disaster Prevention and Management Center about 6 months back and I was very impressed with the facilities and the team headed by Mr Manoj. Kudos to them.
Process Safety - OSHA penalises plastics plant
OSHA has penalized a plastics plant for deficiencies. The article says "The violations include the company's failure to properly contain polyvinyl chloride dust particles; evaluate contractors' safety programs and procedures; properly inspect process equipment; provide fire retardant clothing for employees; require employees to wear adequate eye protection with side shields; provide proper training; and provide employees with an infirmary, clinic, or person trained in first aid. Additionally, inspectors identified hazards involving a lack of machine guarding; a deficient process safety management program; inadequate lockout/tagout procedures for energy sources; and unguarded machinery, floor holes, and walkways. OSHA issues a serious citation when there is substantial probability that death or serious physical harm could result and the employer knew, or should have known, of the hazard".
It is interesting to note that the investigation was launched on the basis of a complaint of an employee! Read the full article in this link.
It is interesting to note that the investigation was launched on the basis of a complaint of an employee! Read the full article in this link.
April 4, 2010
Process Safety - Another day, another blast!
On Good Friday, another blast occurred in a refinery in the USA. The CSB will be investigating the incident but it appears that the CSB is now having its hands full with its investigators currently investigating other incidents. If this is the trend in the USA where PSM is mandatory, we must be very careful in India!
"A Washington state oil refinery hit by a deadly blast and fire early Friday was recently fined for safety violations amid what federal watchdogs call a troubling trend of serious accidents at refineries.
Three men died at the scene and two women died later at a Seattle hospital. Two other men were hospitalized with major burns over the majority of their bodies. It was the largest fatal refinery accident since a 2005 explosion at a BP American refinery in Texas killed 15 people and injured another 170.The Good Friday holiday blast rattled windows more than a mile away and has the most recorded fatalities since 15 workers were killed in a BP Plc incident in 2005 at that company’s Texas City, Texas, operations.
The Tesoro incident occurred as members of a seven-person crew were cleaning a heat exchanger in a unit handling naphtha, a volatile liquid chemically similar to jet fuel, Westfall told reporters.
The blast shook houses and woke people miles away, shooting flames as high as the refinery’s tower before the blaze was extinguished about 90 minutes later.
The blast occurred in a unit that was in the dangerous process of returning to operation, turning up heat and pressure, said Tesoro spokesman Greg Wright".
CSB Chairman and CEO John Bresland said, “The CSB has eighteen ongoing investigations. Of those, seven of these accidents occurred at refineries across the country. This is a significant and disturbing trend that the refining industry needs to address immediately.”
Read the complete article in this link
"A Washington state oil refinery hit by a deadly blast and fire early Friday was recently fined for safety violations amid what federal watchdogs call a troubling trend of serious accidents at refineries.
Three men died at the scene and two women died later at a Seattle hospital. Two other men were hospitalized with major burns over the majority of their bodies. It was the largest fatal refinery accident since a 2005 explosion at a BP American refinery in Texas killed 15 people and injured another 170.The Good Friday holiday blast rattled windows more than a mile away and has the most recorded fatalities since 15 workers were killed in a BP Plc incident in 2005 at that company’s Texas City, Texas, operations.
The Tesoro incident occurred as members of a seven-person crew were cleaning a heat exchanger in a unit handling naphtha, a volatile liquid chemically similar to jet fuel, Westfall told reporters.
The blast shook houses and woke people miles away, shooting flames as high as the refinery’s tower before the blaze was extinguished about 90 minutes later.
The blast occurred in a unit that was in the dangerous process of returning to operation, turning up heat and pressure, said Tesoro spokesman Greg Wright".
CSB Chairman and CEO John Bresland said, “The CSB has eighteen ongoing investigations. Of those, seven of these accidents occurred at refineries across the country. This is a significant and disturbing trend that the refining industry needs to address immediately.”
Read the complete article in this link
Process Safety – “Aging pipe fittings and plant mismanagement – a lethal combination”
An article mentions about aging pipe fittings and mismanagement. It mentions “Even the highest specification pipe fittings will fail, if they are not backed up with competent system management and the correct hardware. Too often, flanges are expected to carry more than their fair share of responsibility in preventing leaks and accidents”.
I have investigated a number of incidents where this exact reason has been the cause of a failure. This is a disturbing trend and it will help if plant management revisit their mechanical integrity program.
Read more of the article in this link
I have investigated a number of incidents where this exact reason has been the cause of a failure. This is a disturbing trend and it will help if plant management revisit their mechanical integrity program.
Read more of the article in this link
Process Safety – Shades of Bhopal?
“Bayer CropScience has agreed to pay a $143,000 fine to resolve safety citations stemming from a fatal explosion at its Institute plant in 2008.
A congressional committee report said the explosion came close to compromising a tank holding methyl isocyanate, or MIC. An MIC leak from a former Union Carbide plant in Bhopal, India, in 1984 killed thousands of people.
Union Carbide once operated the West Virginia plant, now owned by Bayer CropScience. MIC is used in the manufacture of insecticides at four different units at the sprawling 465-acre plant. One unit, the methomyl unit, was damaged in the explosion”.
Read the full article in this link
A congressional committee report said the explosion came close to compromising a tank holding methyl isocyanate, or MIC. An MIC leak from a former Union Carbide plant in Bhopal, India, in 1984 killed thousands of people.
Union Carbide once operated the West Virginia plant, now owned by Bayer CropScience. MIC is used in the manufacture of insecticides at four different units at the sprawling 465-acre plant. One unit, the methomyl unit, was damaged in the explosion”.
Read the full article in this link
Subscribe to:
Posts (Atom)