December 4, 2010
Incident at DuPont plant hospitalises two
Read the full article in this link
Fire in a chlor alkali plant and citations from OSHA
In another development, OSHA has cited Huntsman Petrochemical of Houston Texas of violations in PSM. The article is quoted below:
"OSHA began its investigation June 7 in response to an incident in one of the company’s process units.Alleged serious violations include failing to incorporate operating procedures for all safety devices in the company’s operating guide; adequately train employees in safe operating procedures; properly shut down process equipment; identify and isolate all energy sources to the equipment; and to ensure lockout/tagout energy isolating devices such as line valves prior to employees performing maintenance on the equipment. A serious citation is issued when there is a substantial probability that death or serious physical harm could result from a hazard about which the employer knew or should have known. The company has 15 business days from receipt of the citations to comply, request an informal conference with OSHA’s area director in Houston, or contest the citations and penalties before the independent Occupational Safety and Health Review Commission".
Read the article in this link.
December 3, 2010
Fire in natural gas furnace in ammonia plant
When I was shift in charge in an ammonia plant 30 years ago, we used to light up the start up heater for heating up the ammonia convertor. This furnace was a natural draft and naphtha fuel fired design. We used to keep increasing the firing while closely monitoring the rate of heating up. The pressure in the gas coil was 220 Kg/cm2. The burner flames used to be coming out of the top of the stack during the final phases of heating. Luckily we never had any incident of coil rupture in this heater or otherwise I would not be here today!!
Furnace can Kill if you mistreat them. Read your operating instructions, have your protection systems maintained and conduct periodic inspection of the coils.
Read the article in this link.
Axial misalignment causes a fatigue failure -Quantas A380 incident
The ATSB which is conducting investigations into the engine failure incident that occurred to the Airbus A 380 aircraft on November 2010, has mentioned the following in a safety alert:"A subsequent examination of the aircraft indicated that the No 2 engine had sustained an uncontained failure of the Intermediate Pressure (IP) turbine disc. Sections of the liberated disc had penetrated the left wing and the left wing-to-fuselage fairing, resulting in structural and systems damage to the aircraft. The No 2 engine was removed from the aircraft and disassembled in an authorised engine workshop for examination, under the supervision of the Australian Transport Safety Bureau. In addition, a large section of liberated IP turbine disc was also recovered from Batam Island for examination. Those examinations are ongoing. Recent examination of components removed from the failed engine at the Rolls-Royce plc facility in Derby, United Kingdom, has identified the presence of fatigue cracking within a stub pipe that feeds oil into the High Pressure (HP) / Intermediate Pressure (IP) bearing structure. While the analysis of the engine failure is ongoing, it has been identified that the leakage of oil into the HP/IP bearing structure buffer space (and a subsequent oil fire within that area) was central to the engine failure and IP turbine disc liberation event.
Misaligned stub pipe counter-boring is understood to be related to the manufacturing process. This condition could lead to an elevated risk of fatigue crack initiation and growth, oil leakage and potential catastrophic engine failure from a resulting oil fire".
The lessons from Bhopal – Relevant more so today
1. Do not cut costs without looking at the effects on process safety
2. Maintain all your layers of defense.
3. Continually ensure that competency of personnel operating and maintaining plants are updated and current
4. Be prepared for the worst case scenario.
5. Understand the risks and measures to eliminate / reduce or control them
6. Learn from your past incidents. Those who do not learn are condemned to repeat the incidents.
7. Pay heed to your process safety management system audit reports
Read my older post comparing the Bhopal and the BP incident of 2005 in this link
December 1, 2010
Maintain your mitigation systems - they are your last lines of defense
Read the article in this link
November 30, 2010
Human issues in the Deepwater Horizon blowout
"1.The incident at the Macondo well and Deepwater Horizon MODU was precipitated by the decision to proceed to temporary abandonment of the exploratory well despite indications from several repeated tests of well integrity [the test type known as a negative (pressure) test] that the cementing processes following the installation of a long-string production casing failed to provide an effective barrier to hydrocarbon flow (Sections II and III).
2. The impact of the decision to proceed to temporary abandonment was compounded by delays in recognizing that hydrocarbons were flowing into the well and riser and by a failure to take timely and aggressive well-control actions. Furthermore, failures and/or limitations of the BOP, when it was actuated, inhibited its effectiveness in controlling the well (Sections III and IV).
3. The failures and missed indications of hazard were not isolated events during the preparation of the Macondo well for temporary abandonment. Numerous decisions to proceed toward abandonment despite indications of hazard, such as the results of repeated negative-pressure tests, suggest an insufficient consideration of risk and a lack of operating discipline. The decisions also raise questions about the adequacy of operating knowledge on the part of key personnel. The net effect of these decisions was to reduce the available margins of safety that take into account complexities of the hydrocarbon reservoirs and well geology discovered through drilling and the subsequent changes in the execution of the well plan (Section VI).
4. Other decisions noted by the committee that may have contributed to the Macondo well accident are as follows:
• Changing key supervisory personnel on the Deepwater Horizon MODU just prior to critical temporary abandonment procedures (Section VI);
• Attempting to cement the multiple hydrocarbon and brine zones encountered in the deepest part of the well in a single operational step, despite the fact that these zones had markedly different fluid pressures (because of the different fluid pressures, there was only a small difference between the cement density needed to prevent inflow into the well from the high-pressure formations and the cement density at which an undesirable hydraulic fracture might be created in a low pressure zone) (Section II);
• Choosing to use a long-string production casing in a deep, high-pressure well with multiple hydrocarbon zones instead of using a cement liner over the uncased section of the well (Section II);
• Deciding that only six centralizers would be needed to maintain an adequate annulus for cementing between the casing and the formation rock, even though modeling results suggested that many more centralizers would have been needed (Section II);
• Limiting bottoms-up circulation of drilling mud prior to cementing, which increased the possibility of cement contamination by debris in the well (Section II);
• Not running a bond log after cementing to assess cement integrity in the well, despite the anomalous results of repeated negative-pressure tests (Section II);
• Not incorporating a float shoe at the bottom of the casing as an additional barrier to hydrocarbon flow (Section II); and
• Proceeding with removal of drilling mud from the well without installing the lockdown sleeve on the production casing wellhead seals to ensure the seals could not be shifted by pressure buildup under the seals (Section II).
5. Available evidence suggests there were insufficient checks and balances for decisions involving both the schedule to complete well abandonment procedures and considerations for well safety (Section VI).
6. The decisions mentioned above were not identified or corrected by the operating management processes and procedures of BP or those of their contractors or by the oversight processes employed by the Minerals Management Service (MMS) or other regulators (Sections VI and VII).
7. Currently, there are conflicting views among experts familiar with the incident regarding the type and volume of cement used to prepare the well for abandonment.There are also conflicting views on the adequacy of the time provided for the cement to cure. These factors could have had a material impact on the integrity of the well (Section II).
8. The BOP did not control—or recapture control of—the well once it was realized that hydrocarbons were flowing into the well. Also, both the emergency disconnect system designed to separate the lower marine riser from the rest of the BOP and automatic sequencers controlling the shear ram and disconnect failed to operate (Section IV).
9. Given the large quantity of gas released onto the MODU and the limited wind conditions, ignition was most likely. However, the committee will be looking into reports (such as testimony provided at the MBI hearings) that various alarms and safety systems on the Deepwater Horizon MODU failed to operate as intended, potentially affecting the time available for personnel to evacuate (Section V).
10. The various failures mentioned in this report indicate the lack of a suitable approach for anticipating and managing the inherent risks, uncertainties, and dangers associated with deepwater drilling operations and a failure to learn from previous near misses(Section VI).
11. Of particular concern is an apparent lack of a systems approach that would integrate the multiplicity of factors potentially affecting the safety of the well, monitor the overall margins of safety, and assess the various decisions from perspectives of well integrity and safety. The “safety case” strategy required for drilling operations in the North Sea and elsewhere is one example of such a systems approach (Section VII)
Read the full report in this link.
November 28, 2010
Static electricity and explosives
Apparently the "human vibrations" they are talking about is nothing but static electricity. A static discharge spark can readily detonate primary explosives. From the article, all measures to avoid static electricity generation were reportedly taken. It will be good if the investigation team shares reasons on what caused the accident without breaching confidentiality as it is a defense unit.
Read the Times of India article in this link.
Safety Integrity Levels - Hip or Hype?
November 26, 2010
Blast in cordite factory
Read the articles in these links":
Blast1
Blast2
November 25, 2010
A test tube explosion!
Read the article in this link.
Wikepedia mentions the following:
"Potassium chlorate is often used in high school and college laboratories to generate oxygen gas[citation needed]; it is a far cheaper source than a pressurized or cryogenic oxygen tank. Potassium chlorate will readily decompose if heated in contact with a catalyst, typically manganese (IV) dioxide (MnO2). Thus, it may be simply placed in a test tube and heated over a burner. If the test tube is equipped with a one-holed stopper and hose, warm oxygen can be drawn off. The reaction is as follows:
2KClO3(s) + heat → 3O2(g) + 2KCl(s)
The safe performance of this reaction requires very pure reagents and careful temperature control. Molten potassium chlorate is an extremely powerful oxidizer and will spontaneously react with many common materials. Explosions have resulted from liquid chlorates spattering into the latex or PVC tubes of oxygen generators, as well as from contact between chlorates and hydrocarbon sealing greases. Impurities in potassium chlorate itself can also cause problems. When working with a new batch of potassium chlorate, it is advisable to take a small sample (~ 1 gram) and heat it strongly on an open glass plate. Contamination may cause this small quantity to explode, indicating that the chlorate should be discarded".
For folks operating chemical reactors in the industry, know what you are dealing with!
Trapped inside a pipe for 80 hours
H2S the deadly killer
Now every "technical" malfunction is caused by a "human" malfunction. I have observed many incident reports which do not want to discuss the human issue at all. Its like the saying "we are like that only"!!!
Read the report in this link.
November 23, 2010
Fire in chemical factory at Vadodara
Read another article on the blast in this link
Ammonia leak at Navi Mumbai
Read another article on the accident in this link.
November 22, 2010
Accident in Chemical factory in China
Two of the injured were in serious condition, the report said. In China, considered one of the world's most dangerous places to work, an average of 187 people were killed in work-related accidents on each day in the first half of this year, the government has said'.
Another article mentions that PVC was produced in the plant.While details of the accident are not known, the production of PVC deals with polymerization reactions that must be controlled carefully to avoid the chance of an accident. I have seen plants where batch operations of critical reactions are carried out manually. As experience levels in the chemical industry are coming down drastically, managements must periodically re assess their risk.
Read the article in this link.
November 20, 2010
Lessons in Process Safety Management from aviation incidents
A news article about the Qantas Superjumbo Rolls Royce engine incident it was a “worst case scenario” when one of its four engines exploded. The article reports that the crew were inundated with 50 error messages. However for the pilots, luck was on their side, there was no fire, and they managed to land the plane safely.
''It could have been much, much worse,'' says Richard Woodward, a Qantas A380 captain and a vice-president of the Australian and International Pilots Association. ''It could probably be termed a one-in-100 million event with bits and pieces going everywhere.''
Smith, a two-time chairman of Australia's aviation watchdog, says it was lucky QF32 did not become a repeat of the Concorde crash in 2000.
Smith says that the public has come to expect the impossible - aircraft being fail-safe. ''It is almost like people believe that flying in the air is perfectly safe. Even the most disciplined person can make an error - it is the same with design.''
''One of the things in aviation safety is 'hindsight bias'. It is so easy after an accident to say they should have known,'' says Thomas Anthony, the director of aviation safety at the University of Southern California.
''It is part of the problem of new engines and new aeroplanes. Change is a frequent precondition to error,'' Anthony says. ''When you are changing things you really do need to have a very robust change management process to identify potential problems.''
The above accidents had direct parallels to process safety. Learn lessons from them!
Read the articles in these links
Air India Express Crash
Qantas Superjumbo incident
PS: I have a deep interest in aviation safety as my Dad was a pilot and I have spent many days in the cockpit with him when I was young!
November 19, 2010
The familiar technical and safety failures
"A sorry catalogue of technical, safety and regulatory failures all contributed to the Deepwater Horizon oil spill in the Gulf of Mexico, according to an interim independent report commissioned by the US Department of the Interior and published today.
The oil spill began on 20 April when an uncontrolled release of oil and gas from an underwater well caused an explosion that engulfed the Deepwater Horizon rig, killing 11 crewmen on board. The leak continued until 15 July, releasing about 5 million barrels of oil into the Gulf, the largest accidental marine oil spill in history.
The report highlights a number of failures that led to the accident. It says the well had not been properly sealed with cement and that this allowed oil and gas to escape.
The "pivotal moment" came when workers carried out several pressure tests to check the integrity of the well but ignored the signs that something was wrong, said Paul Bommer, a petroleum engineer at the University of Texas at Austin and a member of the panel of experts that produced the report.
The report says the panel has not yet had time to work out why the blowout preventer, a giant valve on the seafloor which should have stopped the flow of oil as a measure of last resort, failed to activate".
Always, technical as well as safety failures occur for an incident to happen. Just by implementing management systems does not mean you can prevent an incident. Today, there is also a lot of talk about behavior based safety management systems, but as I have mentioned earlier, I am not a fan of this. It needs constant 24X7 safety oriented behaviour by top management, be it budget allocation, decision making, manpower allocation, gauging technical competency to manage cost cutting etc to ensure process safety is managed well.
Read the full article in this link.
November 18, 2010
Do not ignore the warnings!
In a 28-page report released late Tuesday, an independent panel convened by the National Academy of Engineering said the companies failed to learn from "near misses" and neither BP, its contractors nor federal regulators caught or corrected flawed decisions that contributed to the blowout.
Donald Winter, a professor of engineering practice at the University of Michigan and chair of the 15-member study committee, said in a statement that plugging of the well to seal it off for future oil and gas production continued "despite several indications of potential hazard."
No major accident happens without adequate warning. There will be enough signals that some thing disastrous is about to happen. Do not be risk blind. Read the full article in this link.
November 16, 2010
Explosion during hot work
"David Lightfoot, 58, was carrying out welding work on a large container at Indorama Polymers (Workington) Ltd’s site in Siddick. The container housed 380 tonnes of the explosive powder, Terephthalic acid.
The company was prosecuted by the Health and Safety Executive (HSE) following an investigation into the cause of the explosion. Workington Magistrates' Court heard that, on 29 October 2008, Mr Lightfoot was welding a metal component around a two and a half inch diameter hole that had been sealed with a temporary bung, when he was suddenly engulfed by a fireball.
Mr Lightfoot, from Cockermouth, had been welding for around 20 seconds before finding himself surrounded by flames that forced him down to his hands and knees. He and another worker jumped ten feet to the ground to escape the flames but Mr Lightfoot was left with severe burns to his head, face, arms and hands.
The HSE investigation concluded the bung had fallen out, allowing around 15 grams of the explosive powder to escape, which was then ignited by the welding flame, creating the fireball".
Read the full article in this link.
November 14, 2010
Two fatalties in a Year at Dupont facilities
I wish the CSB brings out clearly what went wrong in these two incidents so that it will be a lesson for all of us.
November 12, 2010
Furnace explosion - take care of refractory lining
"A Pennsylvania jury awarded $12.7 million to two men who were severely burned when a metal melting furnace exploded in 2003. The furnace explosion occurred when the liner failed, allowing molten metal to come into contact with a copper coil filled with ethylene-glycol and water. The resulting reaction caused the furnace to explode and spew hot liquid metal across the workplace".
Take care of your refractory lining in furnaces. In my earlier days as shift in charge in an ammonia plant, flames suddenly came out of a reformer furnace due to fallen refractory. It happened all of a sudden and the flames were close to naphtha fuel lines for the burners!We had to scramble to take action and avoid a catastrophe.
Read the article in this link
November 11, 2010
Process safety in the 21st Century
1.The human being will become more and more the focus in process safety. Technical competency of individuals is fast decreasing and job hopping means that process safety knowledge is fragmented in an organisation.
2.Plants are becoming more and more hi tech with control systems and instruments with wireless technology and “smart” technology while the human being is becoming “unsmarter”.
3.As organisation become larger and larger, the management of process safety is getting lost somewhere in between the layers of communication. While leading process safety indicators are good in highlighting problem areas, the focus on these indicators is also human dependent and with directors on boards of companies changing, this focus gets shifted from time to time.
4.There will be Low frequency High Potential accidents happening in large organisations. The BP case is just a teaser. Even in organisations that manage their process safety closely, one slip is enough.Managing to avoid this “slip” will become tougher and tougher in this “flat world”.
5.Fortunately or unfortunately we are in an age of rapid technology change. Plant operators should be careful to select the technologies they need and more importantly to “deselect” the technologies they do not need. One mans bread may be the other man’s burnt toast!
6.To become more and more competitive, organizations are cutting costs. While there is nothing wrong in cutting costs, I see a drastic decrease in in-house competency to assess the technical issues while cutting costs.
7.There will be a number of security issues with chemical plants as control technologies change.
8.Competency of people is becoming a major issue. Simulator training of plant operators may become a legal requirement soon in many countries!
I do not want to bore you with this monologue, but how do we avoid this? Top management must continually have a feel of what is going on at the ground level. There is no better solution that the old fashioned way of walking the talk by periodically meeting people at ground zero and observing what their problems are! I’m signing off…..!
November 10, 2010
Culture of complacency and process safety
The commission's co-chairman William K. Reilly opened the day saying that a "suite of bad decisions" revealed "a culture of complacency" at BP as well as its main contractors Transocean and Halliburton. He concluded the day saying that the deepwater drilling disaster was the result of systemic problems, not isolated ones.Read the full article in this link
Explosion in chemical storage tank during hot work
Update: The tank reportedly was empty but earlier contained vinyl fluoride as per this news article.
November 9, 2010
Disappearing control rooms and process safety
Read the article in this link
November 8, 2010
Explosion and fire in UK factory & Oil Godown in Chennai
An explosion at a Stiller’s toiletries factory in Newton Aycliffe, County Durham that was followed by a large fire. Cause of the fire is not known.See the youtube video in this link.
A rocket firecracker was the source of ignition of a fire in an oil Godown in Chennai, India. The astray firecracker was part of the Diwali festival celebrations! There are many oil storage facilities in India which are very close to populated areas and there is every chance of an accidental source of ignition. Read more of the fire in this link.
November 7, 2010
The Dangers of Hot Work
"An engineer was killed when a 6000-litre tank exploded when he lit a welding torch to repair a seam in the tank. The tank was moved 30 metres in the explosion, and an observer who was standing 2 metres away was thrown to the ground by the blast. The tank had been flushed with water for three days prior to the explosion but this did not remove all the explosive substances.
• A worker was attempting to remove the lid of a 200-litre container that had previously contained lacquer thinners. The drum, which had both bungs in place when the worker applied heat to the lid, hit the roof of the building 6 metres up. The worker received bruising to his hand.
• While removing a cleaning bung from a 70-litre stainless steel boat fuel tank, a worker passed a heated soldering iron over the bung hole. The petrol fumes ignited, throwing the worker on the floor.
• A worker, who had a few moments spare time, began cutting a 200-litre drum to makes a barbecue. He was unaware of the contents of the drum, which exploded when the torch began the cut. He received minor injuries in the incident.
• A worker passed a gas torch to his colleague over the open lid of a bitumen tank, causing an explosion. The worker, who was on top of the tank, received 10% burns to his face and left hand and his leg was broken in three places. The worker on the other side of the tank escaped injury.
• A welding contractor was attempting to fit a tap into a 5000 litre tank. A cut had been started in one end of the tank when it exploded. The tank was turned around and
flipped over. The opposite end of the tank was blown approximately 42 metres, soaring over a stand of trees 12 metres high and landing in a vacant section. The contractor received cracked ribs, a dislocated shoulder, injuries to his collar bone and severe bruising all oyer the body.
There has been no let-up in accidents and many more examples could be given. Remember, all accidents of this type are potentially fatal. Don’t let it happen to you!"
See the booklet in this link(pdf file)
November 6, 2010
Detecting the spark that causes fires and explosions
"In most cases, a spectacular accident must first occur in order to make the public aware of a problem that lurks continually in many areas of industry: the danger of explosions due to electrical sparks. The simplest method to prevent such explosions is called "Intrinsic Safety". The intention thereby is to prevent ignitable sparks from even being created. Up to now, this has only been possible with small devices having a power of up to approx. 2 Watts - thus, above all, in process measuring and control technique.
A new concept that has been developed at the Physikalisch-Technische Bundesanstalt (PTB) in cooperation with industrial partners, increases this limit now up to 50 Watts and thus makes application possible in many more technical fields. The technology which is already being marketed under the name "Power-i"/DART and which is to be launched as an international IEC standard, promises the industry great cost savings".
"For a long time now, end users and manufacturers have wanted a considerably higher active power while at the same time keeping all the positive characteristics of Intrinsic Safety. And this is exactly what the new "Power-i"/DART technology offers. DART here stands for "Dynamic Arc Recognition and Termination".
"Power-i is different from previous concepts", states Udo Gerlach, the project leader at PTB. "The principle of an emergency shutdown is just as simple as it is effective." The safety-related validated, intelligent monitoring system recognizes a spark already while it is forming and then shuts down the system in a controlled and quick manner, before the spark can even become ignitable. "Thus, complex, expensive constructural safety measures can now be replaced with the new technology".
Read the full article in this link.
November 5, 2010
What went wrong - the BP oil rig disaster
November 4, 2010
A+B=**** Hazards of incompatibility
"Last month, an unsuspecting contractor was delivering chemicals to a water treatment plant in Andover, Minn., when he accidentally poured fluorine into a chlorine tank. A chemical reaction was triggered, releasing hazardous fumes and causing the facility to be evacuated. Luckily, the worker only sustained minor injuries and the plant was back in operation just a few hours later, but more serious, and perhaps deadly, consequences could have easily resulted from this simple mistake".
See the full article in this link.
FOR MY READERS FROM INDIA, WISH YOU AND YOUR FAMILY A VERY HAPPY DIWALI!
October 30, 2010
Speech by Jordan Barab of OSHA on Process Safety Management
"First: Effective process safety programs and strong workplace health and safety culture are critical for success in preventing catastrophic events.
Second: Industries need to learn from their mistakes. We know the major causes and we know the remedies. Yet lessons learned are not applied and the same problems surface to threaten workers again and again.
Third -- and I'm not telling you anything you don't already know: Numbers don't tell the whole story. Focusing on low DART rates alone won't protect you from disaster. New metrics are needed.
Now, let's explore these ideas a bit more.
Let's look at Concept number one: Effective process safety management systems and workplace safety culture are critical for success in preventing catastrophic events.
In the Baker Panel Report, issued after the BP Texas City explosion, the panel devoted considerable space to the importance of effective process safety systems and the need to build a strong corporate safety culture.
Process safety failures are typically low-frequency but high-consequence events. Our PSM systems have to be strong, and we cannot wait until we have an incident to discover that they were not.
What it comes down to is organizational culture. To paraphrase Professor Andrew Hopkins (whose work I'm sure you are all aware of): Workplace culture is not just an educational program that gets everyone to be more risk-aware and think "safety first." It's deeper and more ingrained than this. Hopkins and the Center for Chemical Process Safety have defined culture as "the way we do things around here."
What I'm talking about is a set of practices that define the organization and influence the individuals who make up the organization. This kind of pervasive, systemic organizational safety culture must come from the top -- and it must be expressed with transformative action, not just simple slogans.
Next: Concept Number Two: Industry must learn from its mistakes.
For three years now, OSHA has had in place a Refinery Process Safety Management National Emphasis Program. We are deeply troubled by the significant lack of compliance we are finding in our inspections, and with the number of serious refinery problems that continue to occur.
Time and again, our inspectors are finding the same violations in multiple refineries, including those with common ownership -- a clear indication that concerns and findings are not being communicated across corporations or throughout the industry or even within different units in the same refinery.
Consistently throughout the course of the Refinery NEP, we have found that over 70 percent of the citations fall into the top four PSM elements:
• Mechanical Integrity
• Process Safety Information
• Operating Procedures
• Process Hazard Analysis
Let's talk about these top four elements:
1. In MECHANICAL INTEGRITY, problems include failure to perform inspections and tests, and failure to correct deficiencies in a timely manner. This is a particular concern given the aging of refineries in the United States.
2. PROCESS SAFETY INFORMATION, including failure to document compliance with Recognized and Generally Accepted Good Engineering Practices to keep process safety information up to date, and to document the design of emergency pressure relief systems.
3. OPERATING PROCEDURES: failure to establish and follow procedures for key operating phases, such as emergency shutdowns, and using inaccurate or out-of-date procedures.
4. PROCESS HAZARDS ANALYSIS, including lack of attention to human factors and facility siting, and failing to address PHA findings and recommendations in a timely manner -- or, all too often, failing to address them at all.
More than a year ago, OSHA sent a letter to every petroleum plant manager in the country, informing them of these frequently cited hazards. Yet, a year after this letter went out, our inspectors continued to find the same problems in many facilities.
And, finally: Concept Number Three: The problem with numbers.
In any business or organization, one of the problems we find when trying to measure performance is determining how and what we measure.
Unfortunately, as we've discovered, having good numbers on your OSHA 300 logs doesn't correlate with having an effective process safety program.
The classic example of this is BP-Texas City, which had very good injury and illness numbers prior to the 2005 explosion that killed 15 workers and injured 170 others. This tragedy, of course, revealed serious process safety and workplace culture problems at the facility despite the good numbers the company had on paper.
It was noted in press reports that many of the workers killed at BP Texas City had just finished a meeting that touted their safety record. More recently, it was noted in the press that BP executives were on the Deepwater Horizon drill in platform in the Gulf of Mexico, celebrating their excellent safety record shortly before the explosion and fire that led to the deaths of 11 workers. In the days following that catastrophe, company officials continued to wave their low injury and fatality rates as a defense while workers widows planned funerals.
There's a message here: Boasting about favorable safety rates while workers are dying doesn't make a company look like a serious employer; and trade organizations that give awards to their members based solely on a lack of slips, trips and falls doesn't make them look like they are seriously addressing serious problems.
Don't misunderstand me: We need to keep reporting and tracking the numbers -- DART rates are useful -- but employers must not let those numbers lull them into a false sense of security. Looking only at these numbers doesn't warn us about pending doom from cutting corners on process safety
To ensure strong PSM systems, we need to do a better job of identifying useful leading indicators. We all recognize the stock market's investment warning that "past performance is no guarantee of future success." This also applied to the low-frequency, high-consequence events that process safety programs guard against.
The chemical and petrochemical industries must continue to develop and track leading indicators to measure the performance and continuously improve process safety management systems".
In my experience, the points that have been highlighted by the speaker are time and again found lacking in many industries.
Read the full speech in this link
Fire in oil tank
October 29, 2010
An appeal to readers - Share an incident!
October 28, 2010
Do not forget Bhopal!
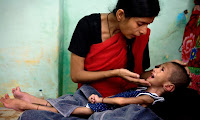
Tasleen, 26, who was poisoned by the Bhopal gas leak, cares for her disabled daughter. Photograph by Alex Masi
Every day, the people working in the chemical industry must realise that process safety is for the good of people - people inside the plant and people outside the plant. The horrors of the Bhopal Gas Disaster continue even today. We should not forget Bhopal. I think it will be a good practice for every chemical plant to organise a"Don't Forget Bhopal" day on December 2nd or 3rd every year and remind all managers of the things that went wrong at Bhopal and the lessons learnt from Bhopal..
See the human impact of Bhopal in pictures in this link.
October 26, 2010
Critical utilities are important for process safety
Read the news article in this link.
The EPA has reported an accident in 1999 involving a plant converting bauxite to alumina in a series of steam-heated pressure vessels. A loss of power stopped all pumps including those that circulated process material through heat exchangers for cooling. However, steam injection stayed on causing temperatures and pressures to increase. Pressure relief valves and piping were blocked or choked with solid deposits hindering their ability to relieve the increasing pressure. Several vessels over-pressured and exploded. The force of the explosion and release of highly corrosive caustic material injured 29 employees and extensively damaged the plant.
October 24, 2010
A third eye for process safety
Now while this is a good idea, it throws up another window regarding security of such networks. Just imagine if someone was able to unauthorizedly break into these networks!
I personally feel that while technology can be an enabler,it cannot solve all problems. Read the full article in this link.
October 23, 2010
The importance of corrosion monitoring and control in Process safety
Read the full article in this link
October 22, 2010
A missing word causes an accident!
October 21, 2010
Disposal of old ammonia gas cylinders
LPG tanker accidents
You can view them in this Link
October 20, 2010
The importance of P & ID's in process safety
October 19, 2010
No Safety, No Moolah!
"The memo, written by new chief executive Bob Dudley, was sent to employees on Monday, the story said.
The sole criterion for judging performance in the 2010 fourth quarter would be "each business's progress in reducing operational risks and achieving excellent safety and compliance standards," said the memo.
The change was designed to ensure an incident such as the "Deepwater Horizon tragedy" never happens again, the story said".
Read the full article in this link. and in this link too
October 18, 2010
Knocked off valve causes ammonia leak
October 16, 2010
Confined spaces are deadly!
See the flyer in this link and please share it with all your employees. It may save a life!
October 15, 2010
Lessons from the Tesoro Refinery Blast Investigation
•On April 2nd,2010 early morning, a blast at the Tesoro refinery in Anacortes, USA, occurred killing 7 personnel. The blast occurred due to the catastrophic failure of a feed effluent exchanger in the naphtha hydrotreating unit during start up. The exchanger was about 40 years old. The original refinery was started in 1950’s by Shell. Shell sold the refinery to Tesoro in 1998. The failed heat exchanger was not tested for last 10 years. Tesoro had planned an inspection in 2008 but did not carry it out.
•6 out of 7 personnel who died were not trained in the start up procedure.
•The frequency of Tesoro Refinery's inspection of the feed effluent exchanger was not consistent with applicable manufacture's recommendations, good engineering practices, and or prior operating experience.
•The Tesoro Refinery did not correct deficiencies associated with effluent exchanger shell and tube side warm up lines before further use or in a safe and timely manner
•Tesoro Refinery did not correct deficiencies associated with effluent exchanger companion flanges and temporary clamps before further use or in a safe and timely manner when the necessary means are taken to assure safe operation. (flanges were leaking during start up and steam lances held by personnel were used to dilute the leaks)
•Tesoro Refinery did not develop and implement written procedures for startup following turnaround, or after an emergency shutdown of exchangers that provided clear instructions for safely conducting activities involved in the process consistent with the process safety information that addressed steps for each operating phase.
•Tesoro Refinery did not establish and implement written procedures to manage the change made to the warm up steps during the March 2009 start up and those conducted in February and March of 2008 on the E6600 effluent exchangers.
•Tesoro Refinery did not establish and implement written procedures to manage the changes made to the operating limit minimum hydrogen oil ratio feed to Naphtha Hydrotreater.
•Tesoro Refinery did not establish and implement written procedures to manage the change made by placing mechanical clamps on the companion flanges between effluent exchangers E-6600 A/B and D/E on or about March 2009.
•Tesoro Refinery did not establish and implement written procedures to manage the change made by placing the Anacortes Corrosion Awareness and Management Program (ACAMP) on hold indefinitely beginning the third quarter of 2004.
•Tesoro Refinery did not establish and implement written procedures to manage the change made by discontinuing the process hazard analysis revalidation system that included mechanical integrity and corrosion control review in 2006.
•Tesoro Refinery did not establish and implement written procedures to manage the changes made by temporarily or permanently suspending inspection procedure I-08.07 on or about September 2009
•The Tesoro Refinery did not ensure that the 2006 Process Hazard Analysis Revalidation was consistent with the current process.
•The Tesoro Refinery did not update process safety information following changes made to the effluent exchangers on or about December 2005.
•The Tesoro Refinery did not investigate each incident which resulted in, or could reasonably have resulted in, a catastrophic release of highly hazardous chemicals in the workplace. Failure to investigate incidents could result in their recurrence and cause serious injury or death.
•Tesoro Refinery did not ensure that appropriate checks and inspections were performed to assure that equipment, such as the warm up lines and replacement tube bundle, were installed properly and consistent with the design specifications. Lack of quality assurance inspections and checks could lead to improper installations of process equipment and result in serious injury or death.
•Tesoro Refinery did not ensure that maintenance materials, spare parts and equipment were suitable for the process application for which they will be used, such as the bellows assemblies.
•Tesoro refinery did not ensure that all emergency responders and their communications were coordinated and controlled by the Incident Commander (IC).
•Tesoro Refinery did not assure that all Fire Brigade members were fully trained prior to the incident response on the morning of April 2nd, 2010.
Read the full citation in this link.
October 14, 2010
Process safety and the Stuxnet worm
The worm, designed to attack Siemens industrial control systems, has not spread widely. However, it has affected a number of Siemens plants, according to company spokesman Simon Wieland. "We detected the virus in the SCADA [supervisory control and data acquisition] systems of 14 plants in operation but without any malfunction of process and production and without any damage," he said in an e-mail message".
As technologies become more and more complicated, chemical plants are also becoming susceptible to attack through the software and other technologies they use. Do not be complacent about your plant software security systems. Many chemical companies ban USB sticks inside their premises.
Read more of the article in this link.
Cost Vs Process Safety - the perennial question
That's as wishful -- and seemingly irresponsible -- as the response another BP engineer had given Halliburton before the disaster, saying that "hopefully the pipe stays centralized due to gravity."
BP engineers knew they were dealing with a difficult well and that more than 120 workers were at the Deepwater Horizon rig. Why, then, would BP personnel be so seemingly cavalier about a crucial part of the process? Mr. Walz and Mr. Guide may have provided the answer when they said BP employees are graded every year based on how much money they save the company".
Read the full artcile in this link.
Stronger Safety after an incident!
"Incoming BP boss Bob Dudley has announced the creation of a new safety division along with a management reshuffle that includes the departure of Andy Inglis, the head of the oil firm's key exploration and production division.
The group said the safety division would have "sweeping powers" to oversee and audit the company's operations around the world with the safety and operational risk department having authority to intervene in all aspects of its technical activities.
The powerful organisation is designed to strengthen safety and risk management across the group, following the Gulf of Mexico disaster that caused the biggest oil spill in US history. It will be headed by Mark Bly and report directly to incoming chief executive Dudley, who replaces Tony Hayward on Friday.
Dudley said: "These are the first and most urgent steps in a programme I am putting in place to rebuild trust in BP – the trust of our customers, of governments, of our employees and of the world at large. That trust is vital to the restoration of shareholder value which has been so adversely affected by recent events.
"Our response to the incident needs to go beyond deepwater drilling. There are lessons for us relating to the way we operate, the way we organise our company and the way we manage risk."
It is good that BP is reorganizing its safety functions. But in many companies, I keep hearing from the existing safety department that line managers do not pay heed to what they say! Look inwards into your organization and see if you are listening to you existing safety managers! They will have a lot to tell you. In fact prior to the BP Texas refinery disaster, it is reported that the safety manager had put up a slide on the key risks in which he mentioned "BP Texas refinery kills someone in the next few months"!
Read the news article in this link
October 8, 2010
H2S leak at Refinery
Read another article about the leak in this link.
October 6, 2010
Toxic sludge flood disaster in Hungary
Read more in these links:BBC1 , BBC2
Deadly chemical reactions
October 5, 2010
Process Safety - Old is Gold If.....
The article mentions the following:
"On Monday, Silverstein said his inspectors determined the Anacortes accident was caused when a 40-year-old steel heat exchanger ruptured and spewed vapor and liquid that immediately exploded. Tests showed welds in the exchanger had developed cracks over the years. The rupture occurred along those weak points as the equipment was coming back online after maintenance.
Tesoro hadn't properly inspected the exchangers since 1998, and even then didn't test the most vulnerable areas, Silverstein said. Tesoro had planned to test them in 2008, but never did.
"If they had, we believe, they would have found the cracks that caused this explosion," Silverstein said. "They would have prevented this horrible incident from ever happening."
All seven workers who died had been standing near the exchangers. They were there in part, Silverstein said, because Tesoro had been unable in recent years to stop the equipment from leaking volatile, flammable gases.
So employees were positioned around the machinery in hard hats, gloves and goggles with "steam lances" — long tubes — they used to disperse the vapors. They also had to manually adjust valves during startup to make sure leaks didn't get out of control.
Read the full article in this link
The Human and Process Safety
"The San Bruno natural gas explosion has underscored a growing concern about the capabilities of utility employees who watch over the nation's pipelines and whose errors have been linked to a number of mishaps, some of them catastrophic.
The National Transportation and Safety Board has said among the questions it is investigating is whether workers at a PG&E pipeline-monitoring terminal in Milpitas were fatigued or poorly trained. And just eight days after the Sept. 9 blast, the federal Pipeline and Hazardous Materials Safety Administration moved to speed up adoption of a rule to insure that workers doing similar jobs at companies across the country are well-trained and rested -- especially since many of those workers put in 12-hour shifts".
"A 2005 NTSB study that scrutinized 13 pipeline mishaps involving various liquids from 1992 to 2004 found that "in ten of these accidents, some aspect of the SCADA system contributed to the severity of the accident." In many cases, the problems were aggravated when workers monitoring the systems failed to quickly recognize and respond to leaks. Among the accidents cited:
# An April 7, 1992, fire in Brenham, Texas, that caused three deaths and 21 injuries after a poorly trained worker failed to notice the changing pressure in a pipe, in part because the system didn't display data in a way the worker could easily interpret.
# On June 10, 1999, a worker failed to realize that a gasoline pipeline had ruptured and burst into flames in Bellingham, Wash., because the malfunctioning control system was providing erroneous data. As a result, it took more than an hour to shut the pipe's valves. Three people died and eight were injured.
# On Oct. 27, 2004, after a pipeline containing the caustic and potentially deadly chemical anhydrous ammonia ruptured in Kingman, Kansas, a worker misinterpreted alarms generated by a control system and mistakenly increased the flow of ammonia into the line. No one was killed or injured, but 204,000 gallons of the liquid flowed into a creek, killing more than 25,000 fish, including some threatened species.
"From 1990 to 2009, gas-line operator errors caused a little more than 5 percent of all the significant accidents nationwide, resulting in 8 fatalities, 150 injuries and $16.2 million in property damage, according to data kept by the Pipeline and Hazardous Materials Safety Administration. During the same period, operator error caused 11.5 percent of "serious incidents," which involve a fatality or an injury requiring hospitalization".
Read more of the article in this link.
October 4, 2010
Flammable gas detectors - use them properly
October 2, 2010
Explosion in Fertiliser plant in USA
October 1, 2010
Don't underestimate the power of water!
Read about the failure in this Wikepedia link.
See amazing photos of the disaster in this link.
September 30, 2010
Chlorine Gas leak reported from pipe
While I am not commenting on the cause of the leak, if you have pipes carrying hazardous chemicals crossing roads through culverts, ensure that they are inspected for corrosion and thickness reduction. Especially vulnerable are the drain and vent points. Your mechanical integrity program must cover this.
Natural gas pipelines - emergency isolation valves
In any pipeline transporting hazardous material, remotely operated emergency isolation valves must be provided to immediately isolate the supply of the hazardous material safely. Also, test them to ensure they are in operating condition.
Read the full article in this link
September 29, 2010
Control systems - do not complicate things!
I strongly believe in the principle that WE HAVE TO KEEP IT SIMPLE YET FUNCTIONAL!
Why do we have to complicate things and then work on uncomplicating them?
Read an article on the dangers that are brought on by newer technologies and control systems in this link
September 27, 2010
Run to failure or run to safety?
Mr Rafael Moure Eraso chair of the US Chemical Safety Board said that "We see a growing crisis of safety in the oil sector." He cited the Gulf rig disaster as well as recent explosions and fires at onshore production, processing, and refining facilities.
Mr Beevers said that the industry needs to bring back shorter periods between turnovers, which are times when a refinery is shut down for maintenance.
Mr Moure Eraso said that operators have told him that turnarounds that normally occur every two to three years are happening now every four to five years. They have said that broken equipment is not immediately addressed and workers are told to work around the problem".
This is a classical production Vs Safety question. How do you decide the intervals between planned shutdowns for maintenance? Of late, due to market pressures, many organisations are increasing the duration between shutdowns.In the interest of process safety, this decision has to be made very carefully after weighing all options, including ageing of the plant,process incidents and maintenance data.
Read the full article in this link.
September 24, 2010
Oil fire in pipeline in China
September 22, 2010
Overfilled rail tanker "burps" isobutane!
Read more of the news and see the video in this link.
Process safety - Its lonely at the top!
The best time to consider these issues is long before the adverse critical incident occurs. Most state laws require indemnification of employees charged with wrongdoing during the course of their employment, as long as those employees are ultimately exonerated. In addition, broad corporate indemnity provisions and directors and officers (D&O) insurance policies are available to protect such employees".
Read the full article in this link
September 20, 2010
The human consequences of a fire accident
September 19, 2010
Running blind - the dangers of reactive chemistry
OSHA warns power plant operators on hazards of natural gas purging
Hazardous chemicals lying in Indian Ports
September 14, 2010
Pesticides - safety and health information
Fire in GAIL plant kills one
Abhay Gujar also sent the news that the fire occurred in the crude hexane reboiler in unit-1 during a routine maintenance operation.
Hope the oil industry safety directorate investigates the incident and puts up the reasons for the incident on their website....
September 12, 2010
Narural gas pipe explosion inUSA
"The force of the explosion was large enough to level the area immediately around the blast’s epicenter. NTSB teams, as well as local investigators, are combing through the blast zone looking for evidence that will allow them to determine the cause. The primary problem with useful evidence in a fire investigation is the simple fact that much of it burns up during the event. Therefore, investigators have to look beyond the physical evidence to gain insight as to what really went wrong. Investigators are looking at the maintenance and safety records of the gas main in question, to see if red flags appear. They are also looking into the personal records of all individuals who worked on that particular section of pipe. This includes, drug problems and the general performance records of key individuals involved in the pipe’s maintenance.
Once the gas main has been designed and stringent regulations have been met, it’s up to qualified contractors to safely install the pipe. Lengths of pipe are specially welded together by trained pipe welders and this presents a potential problem. Anytime there is human interaction in the process of building something, the question arises; did that individual do their job correctly? The same holds true for the entire construction process. There have been numerous construction related disasters that were caused by insufficient materials, poor safety regulations and cost cutting. While there is no indication that these forces are at work here, the question still arises, was human error the driving factor in this accident? Mathematically, the odds are sadly in favor of human error".
Read the article in this link
How good and robust are your natural gas line inspection procedures? Are they getting implemented?
September 11, 2010
Abandoned cylinders and now abandoned tanks!
September 10, 2010
Ammonia transfer hose leak incident
BP oil rig disaster internal investigation report
It may also be appropriate for BP to consider further work to examine potential systemic issues beyond the immediate cause and system cause scope of this investigation. The summary of the report findings are given below:
1. The investigation team concluded that there were weaknesses in cement design and testing, quality assurance and risk assessment.
2. The investigation team concluded that hydrocarbon ingress was through the shoe track, rather than through a failure in the production casing itself or up the wellbore annulus and through the casing hanger seal assembly.
3.The investigation team has identified potential failure modes that could explain how the shoe track cement and the float collar allowed hydrocarbon ingress into the production casing.
4.The Transocean rig crew and BP well site leaders reached the incorrect view that the test was successful and that well integrity had been established.
5.The rig crew did not recognize the influx and did not act to control the well until hydrocarbons had passed through the BOP and into the riser.
6.If fluids had been diverted overboard, rather than to the Mud gas separator (MGS), there may have been more time to respond,and the consequences of the accident may have been reduced.
7.The design of the MGS system allowed diversion of the riser contents to the MGS vessel although the well was in a high flow condition. This overwhelmed the MGS system.
8.The heating, ventilation and air conditioning system probably transferred
a gas-rich mixture into the engine rooms, causing at least one engine to overspeed, creating a potential source of ignition.
9.Through a review of rig audit findings and maintenance records, the investigation team found indications of potential weaknesses in the testing regime and maintenance management system for the Blow out presenter (BOP).
Point no. 8 is a repeat of the ignition source in the BP Texas city refinery explosion where a pick up truck took in vapours through its air intake and triggered the initial explosion.Are we learning from our incidents?
Read the executive summary of the report in this link.
September 9, 2010
Oleum gas leak
September 8, 2010
The BP oil rig disaster
What were the underlying causes of the disaster?
• Complacency and routinism; the tendency of those within a large organisation to avoid testing established policies.
• “Bean-counteritis”; a failure to examine constraints on risk management budgets.
• Collectivism; a conviction that existing company policy is, by definition, the best that could possibly be. In American parlance, this is often called “drinking the company Kool-Aid.” It entails a rejection of rigourous analysis of internal management systems,and their appraisal for possible deficiencies.
• A failure, from top to bottom, to subject these systems to outside scrutiny, in the manner of the International Maritime Organisation’s Member State Audit Scheme.
• A tendency to stigmatise concern for the environment as something repugnantly radical, “Greenpeace Socialism”, “tree-hugging”, etc.
• Most significantly, the failure to establish a risk control or safety awareness mindset at all levels of the corporate hierarchy,particularly at middle-management levels, and to effectively offset a “get it done, at the lowest possible cost” attitude at the “coalface”.
Read the full presentation in this link
Fireworks factory blast in Malta
Read the article in this link.
September 6, 2010
Fire in a parcel van in a train due to hexane
September 4, 2010
Caustic soda and process safety
Caustic soda is a also a basic feedstock used in the manufacture of a wide range of chemicals. The Dow Chemical Co. has useful data on process safety aspects related to storage and its design.
Please see the following links:
General storage system guidelines
Storage tank design guidelines
Piping systems
Another fire in oil rig
September 2, 2010
Bhopal and BP – different approaches – different people
Read the full article in this link.